Wood and Tubacex Group enter into global cooperation agreement.
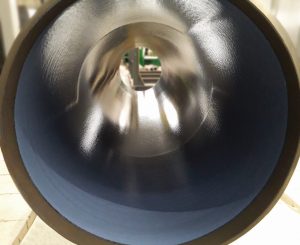
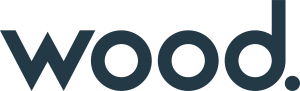
Tubacex Group, the global leading supplier of premium tubular solutions in advanced materials, has entered into a new, five-year cooperation agreement with global consulting and engineering company Wood. The agreement focuses on promoting the disruptive Tubacoat Technology in delayed coker furnaces and other refinery units aligning with the ambition of both companies to unlock reliable and proven solutions for the downstream and refinery sector.
The Tubacoat Technology, developed by Tubacex Group, is based on tailor-made ceramic coatings that allow customers that are faced with severe fouling, coking, corrosion or abrasion challenges in harsh media and high temperature conditions to drastically improve their efficiency, reliability and productivity, while decreasing their environmental impacts.
With this agreement Wood will use its engineering and project execution expertise to deploy the Tubacoat Technology with Wood’s delayed coker technology SydecSM to further improve energy efficiency and availability for both existing and new units.
Brian McCarthy, Vice President of Technology and Products at Wood, said: “We are excited about this cooperation agreement. Wood is well positioned to deliver differentiated success by leveraging its embedded global project implementation capabilities, engineering, and technology, combined with Tubacoat technology, to offer anti-coking solutions for refinery fired heaters in delayed coker, crude distillation unit (CDU) and vacuum distillation unit (VDU) furnaces”.
Jesús Esmorís, CEO of Tubacex Group said “We are pleased with this cooperation agreement. With ongoing initial project opportunities, the agreement has the potential to bring best of technologies from both companies to deliver impactful solutions to existing and new Delayed Coker and other refining units around the world. TUBACOAT tubes minimize formation, deposition and plugging due to coke/carbon in Delayed Coker and other refinery and petrochemical unit furnaces besides minimizing corrosion and thus improve unit reliability, life cycle, throughput and reduced carbon footprint”.
The Pipeline & Gas Journal (PGJ) has selected TUBACOAT
Houston, TX August 2022 – The Pipeline & Gas Journal (PGJ) has selected TUBACOAT as one of the finalists for the PGJ Awards 2022, The awards program honors the energy segment’s leading innovations, as well as outstanding personal contributions to the industry.
Tubacoat is contending with other industry leaders for the Best Coating/Corrosion Advancement Technology 2022 Award. The category recognizes an advancement made during the year in the area of coating and corrosion prevention that extends the life and safety of infrastructure.
Among the finalists, companies such as Sherwin-Williams, GTP Industries, ChampionX, among others. Tubacoat presented its Case Studies for Hot Vanadate Ashes Corrosion on Heat Recuperators and its improvements on performance and reduction of operational cost.
The Award Ceremony will be on November 17, 2022 at the Westin Galleria Hotel in Houston, TX
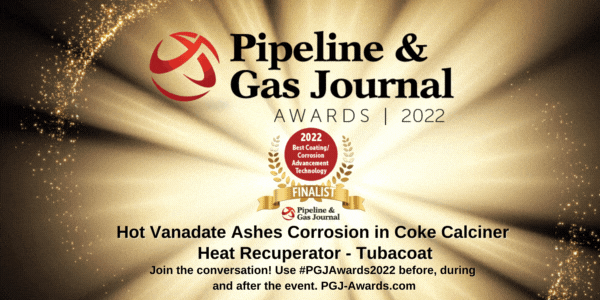
Technical article at Heat Exchanger World Magazine (September 2021)
In most refining conversion units, such as delayed coker and others, unscheduled shutdowns, high maintenance, higher fuel consumption and throughput reduction are common problems. This is mostly due to furnace tube coking, fouling and corrosion.
Ceramic coating technology minimizes formation, deposition and plugging due to coke/carbon in addition to reduction in fouling, corrosion and fuel usage. Use of ceramic coating in these applications leads to longer runs, incremental life cycle for equipment, reliable operations, reduced fuel consumptions and hence significant savings in OPEX and CAPEX.
Tubacoat tubes (advanced ceramic coated tubes) are a disruptive innovation technology from Tubacex Group. This new technology of silica ceramic coating has an excellent resistance to coking, erosion and corrosion at extreme conditions and high temperatures up to 800°C (1472°F) in critical refinery and petrochemical process equipment. Tubacoat tubes also minimize coke formation, deposition and plugging due to their chemical inertness in delayed coker, visbraker, vacuum distillation unit, resid hydrocracker and other refi nery unit furnaces. These benefi ts improve unit run lengths, unit reliability, heat transfer effi ciency, and tubes life cycle without the same level of need for decoking,
and they increase throughput and reduce carbon footprint for both new and aging plant equipment.
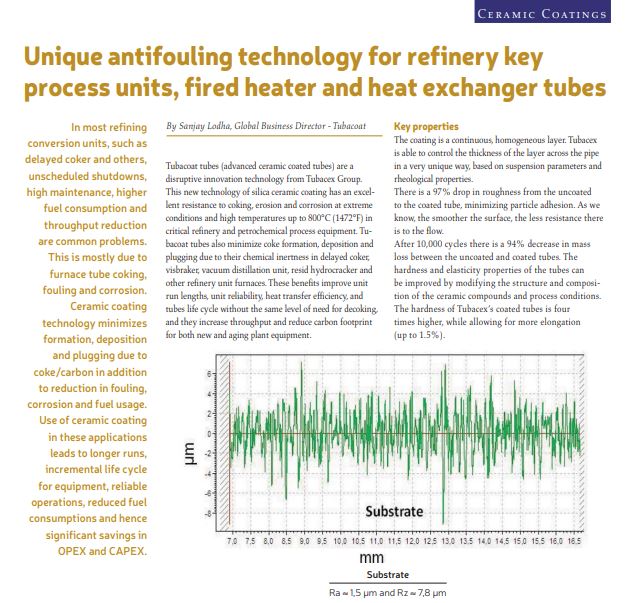
Tubacoat technology implemented in one of the 3 largest Delayed Cokers in the world
At one of the most modern and complex refineries in Asia (11+ Nelson complexity index) they have decided to apply Tubacoat technology in their Delayed Coker Unit, which is one of the 3 largest worldwide. Tubacoat internal coated tubes were successfully installed in October 2020 in of one of their furnaces. Cost savings, increased reliability and improved heat transfer efficiency are the factors which motivated their decision.
Coating of the whole radiant section is expected to save the refinery over 10 million USD/year, based on the reduced number of decoking shutdowns needed and increased throughput.
With this project Tubacoat expands its reference list for fired heater anti-coking applications, which include Vacuum Distillation Units, Visbreakers and Delayed Cokers.
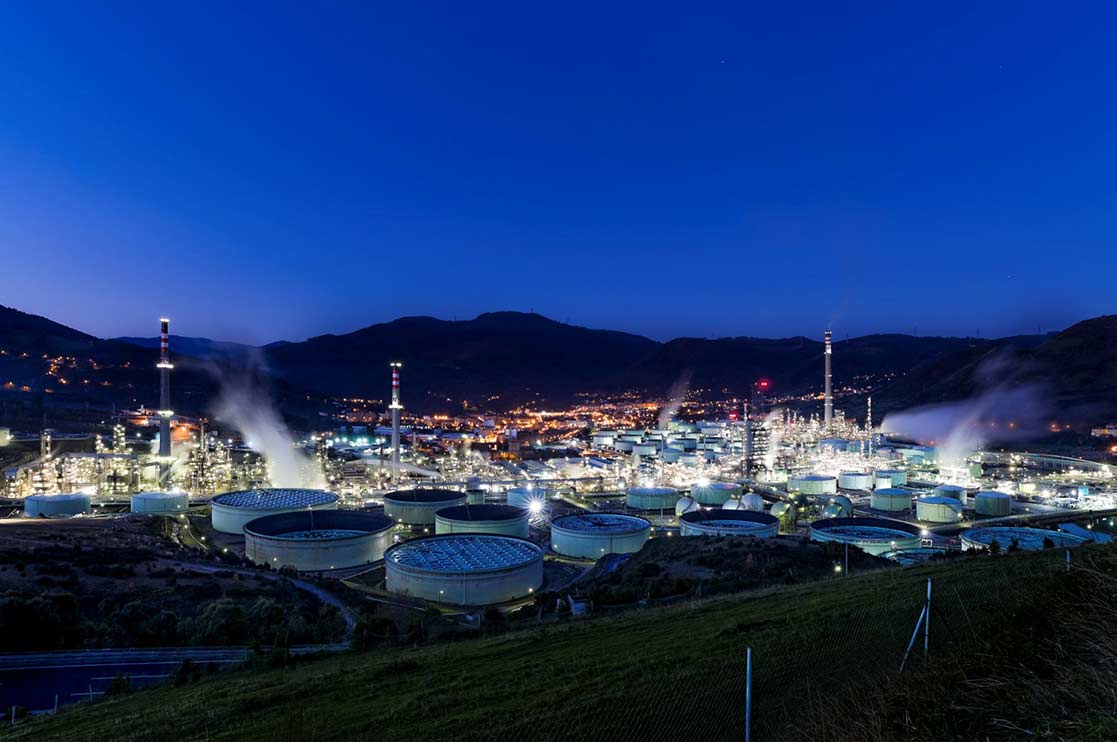
Tubacoat participates in RefComm® Global Virtual Conference 2020
RefComm® is recognized as the world’s premiere Delayed Coking (DCU) conference. Last year’s event, held in Galveston TX, attracted 182 refiners and over 400 exhibitors and suppliers. This year the international delayed coking conference moves online, where refinery operators will be able to learn how Tubacoat technology could benefit their operations.
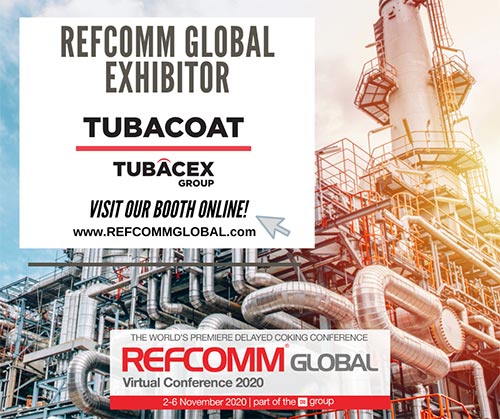